
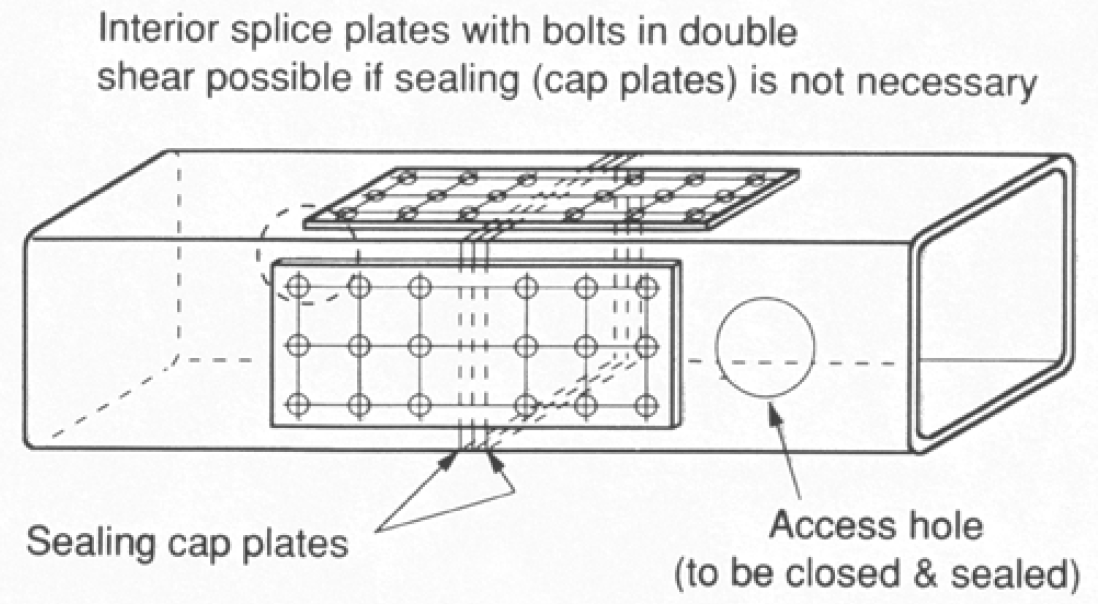
For a simple 90° T‐joint the LRFD resistance of a single weld is given by: The design of fillet welds in structural steel buildings in the US is governed by AISC 360‐10 Table J2.5 and is based on the limit state of shear failure of the weld using a matching (or under‐matching) filler metal.
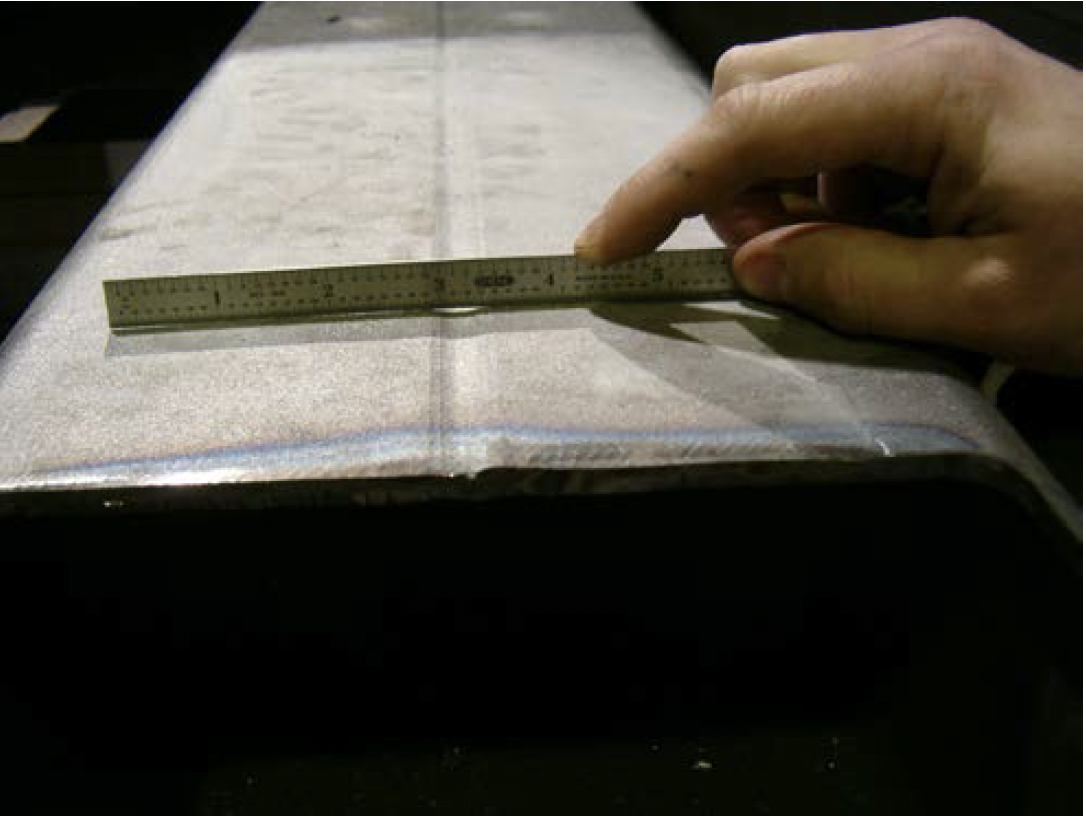
2, are given in AWS D1.1 (2010).įillet welds, being the least expensive and easiest weld type, are the preferred and most common weld type for HSS connections. Prequalified joint details for PJP welds to HSS, particularly for the longitudinal welds in “matched box” connections as in Fig. Partial‐Joint‐Penetration groove welds are an option for HSS connections, especially if fillet weld sizes become large (leg sizes over about ½ in.) and the branch member is reasonably thick. In this case the tapered nose of the casting inserted into the HSS or pipe essentially serves as backing.įigure 2: Macro‐etched PJP groove weld in a matched‐width (β=1.0) HSS connection One exception that comes to mind is for a round HSS welded to a proprietary steel special‐purpose casting – the High‐Strength Connector by Cast Connex Corp., used with diagonal HSS braces in seismic load‐resisting braced frames (shown in Fig. Three basic types of welds account for practically all structural weld joints, including those between HSS: complete‐joint‐penetration (CJP) groove welds, partial‐joint‐penetration (PJP) groove welds, and fillet welds.Ĭomplete‐Joint‐Penetration groove welds (from one side and without backing) are extremely expensive, require specially qualified welders, and should almost never be specified for HSS connections. As member selection is intimately tied to connection capacity, and most HSS connections are required to be unreinforced, it is clear that checking the connection capacity is the responsibility of the structural engineer.

These conditions will generate a truss‐type connection with a high static strength (and a high fatigue resistance too). In addition, the branch thickness‐to‐chord thickness ratio (τ) should be relatively low less than unity, with a value of 0.5 being a good target.
WELDING OF HSS SQUARE FULL
(An exception to this recommendation are connections in Vierendeel frames, where matched‐width HSS are typically necessary in order to achieve full moment capacity). For truss‐type connections, the branch width‐to‐chord width ratio (β) should be relatively high (say 0.7 to 0.8), but still preferably enable the branch to sit on the “flat” of the main member if it is a square/rectangular HSS. This increased flexibility of the connecting face tends to cause an uneven load distribution in the welded joint.Īn important first step is to have selected the members in an HSS connection astutely. Second, the main HSS member face to which a branch is welded is generally much more flexible than its wide‐flange counterpart, as the two webs of the main member (which act as stiffeners) are at the outside of the connection rather than in the middle, as would be the case with a W‐shape web. Unlike open sections, where welding is typically possible from both sides of an element, welding of HSS is only possible from one side, thus requiring larger weld sizes. The welding of Hollow Structural Sections (HSS) does have some unique features. Research Assistant, Department of Civil Engineering, University of Toronto, Ontario, Canada Bahen/Tanenbaum Professor of Civil Engineering, University of Toronto, Ontario, Canada
